Have you ever wondered what makes giant industrial motors, large-scale lighting systems, or even your building's HVAC system spring to life with the flip of a small switch? The AC contactor.
In this comprehensive guide, we'll walk you through everything you need to know. We’ll cover what an AC contactor is, how it works, its key applications, and most importantly, how to choose the right one for your needs. Let's dive in.
What is an AC Contactor?
At its core, an AC Contactor is an electrically controlled switch designed to handle high-current electrical circuits. Think of it as a heavy-duty relay or a remote-controlled light switch on steroids.
Its primary job is simple but critical: to safely make or break the connection between a power supply and a high-power load, like a large motor.
The magic of a contactor is that it uses a very small electrical signal (the control circuit) to manage a much larger, more powerful flow of electricity (the power circuit). For instance, a simple 24V signal from a PLC (Programmable Logic Controller) can activate a contactor that controls a 480V, 100-amp motor. This separation is the cornerstone of modern electrical safety and automation.
What Does an AC Contactor Do?
So, why can't we just connect a big motor directly to a switch? The simple answer is safety and control. An AC contactor performs several vital functions that a simple switch cannot.
1.High-Power Switching: Standard switches would melt or create dangerous electrical arcs if used to control the high inrush currents of large motors or lighting banks. Contactors are built with robust materials and arc suppression features specifically to handle these demanding loads, turning them on and off thousands, or even millions, of times without failure.
2.Remote and Automated Control: This is where contactors truly shine. Because they are activated by a low-power electrical signal, they can be controlled from a distance. This allows an operator to safely start a machine from a control panel or a computer to automatically manage a complex process, like a factory assembly line or a building's climate control system.
3.Safety Isolation: The most important function is protecting both equipment and personnel. The contactor creates a physical gap (an air gap) between the low-voltage control circuit and the high-voltage power circuit. This ensures that any electrical faults, like a power surge on the motor's side, won't travel back and destroy the delicate and expensive control electronics (like a PLC).
Components of an AC Contactor
To truly understand how a contactor works, you need to know its three essential parts.
● The Coil or Electromagnet: This is the control center. It's a coil of wire wrapped around an iron core. When a small control voltage (AC or DC) is applied to the coil's terminals (usually labeled A1 and A2), it creates a powerful magnetic field. This magnetic force is what drives the contactor's switching action.
● The Contacts : These are the components that actually carry the electrical current. There are two types:
○ Main Contacts: These are the large, heavy-duty contacts that connect the power supply to the load. They are typically "Normally Open" (NO), meaning the circuit is broken until the coil is energized.
○ Auxiliary Contacts: These are smaller contacts used for control logic. They can be Normally Open (NO) or Normally Closed (NC) and are used for tasks like sending a "motor is running" signal back to a control panel or preventing two contactors from being on at the same time (interlocking). The contact materials are crucial for performance, often using silver alloys like silver tin oxide for their high conductivity and resistance to arc damage.
● The Enclosure or Frame: This is the protective housing that holds everything together. It insulates the live parts, protects the internal components from dust, oil, and moisture, and prevents accidental human contact. Modern enclosures, like those on our WTAIDQ CJX2D series, are often made from high-performance, flame-retardant polymers that meet strict safety standards.
Applications of AC Contactors in Electrical Systems
You'll find AC contactors in a surprisingly wide range of applications, from small commercial buildings to the largest industrial facilities. Here are some of the most common uses:
● Motor Control: This is the most classic application. Three-pole contactors are the standard for starting, stopping, or reversing three-phase AC motors that power everything from conveyors and pumps to industrial mixers and fans.
● Lighting Control: For large areas like stadiums, parking lots, or warehouses, you can't just use a standard light switch. Contactors are used to control entire banks of high-power lights simultaneously from a single point.
● Heating, Ventilation, and Air Conditioning (HVAC): Contactors are essential in HVAC systems for switching compressors, fans, and electric heating elements. Definite Purpose (DP) Contactors, which we also manufacture, are specifically designed with the ratings and durability needed for these demanding applications.
● Capacitor Banks: In industrial facilities, contactors are used to switch capacitor banks on and off to improve power factor, reducing energy costs. Special capacitor switching contactors are designed to handle the very high initial inrush current.
● Emerging New Energy Systems: As "New Energy Electrical Specialists," we're seeing a huge surge in the use of contactors in modern applications like Electric Vehicle (EV) Charging Stations. Here, they safely connect the high-power AC supply to the vehicle for charging, ensuring a secure and reliable connection every time.
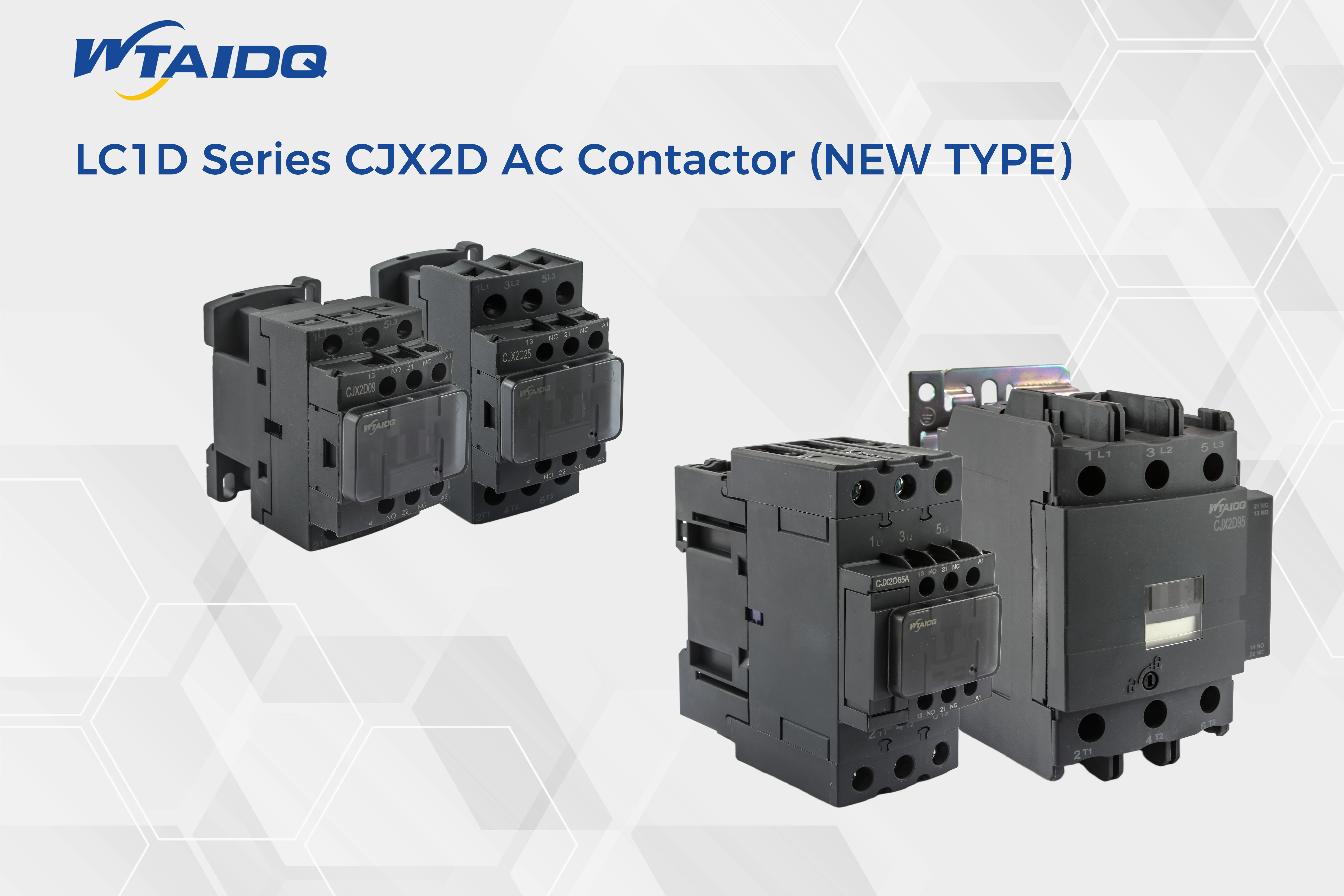
Key Factors to Choosing the Right AC Contactor
Selecting the wrong contactor can lead to premature failure, equipment damage, or a serious safety hazard. It’s not a one-size-fits-all situation. Here are the key factors you must consider, a process we guide our own clients through every day.
1. Voltage Rating (Power Circuit): The contactor's voltage rating must be equal to or greater than the system voltage it will be switching. If you are controlling a 480V motor, you need a contactor rated for at least 480V (often rated for 600V or 690V for a safety margin).
2. Current Rating (Amperage): This is critical. The contactor’s current rating, measured in amps (A), must be able to handle the motor's Full Load Amps (FLA). You should always select a contactor with a current rating slightly higher than the motor's FLA to handle heat and minor overloads.
3. Number of Poles: This refers to the number of main contacts.
● 1-Pole & 2-Pole: Used for single-phase loads, common in residential and light commercial HVAC.
● 3-Pole: The most common type, used for three-phase motors.
● 4-Pole: Used to switch all three phases plus a neutral wire.
4. Utilization Category (AC-1, AC-3, etc.): This code, defined by the International Electrotechnical Commission (IEC) standard 60947, tells you what kind of load the contactor is designed for. This is a detail many people overlook.
● AC-1: For non-inductive or slightly inductive loads, like resistance heaters or lighting.
● AC-3: For starting standard squirrel-cage motors, the most common motor type.
● AC-4: For heavy-duty motor applications involving frequent starting, stopping, and "jogging" (inching), like in cranes.
A contactor's AC-3 rating will always be lower than its AC-1 rating because starting a motor is much harder than powering a heater.
5. Coil Voltage (Control Circuit): The coil voltage must match the voltage supplied by your control system. Common coil voltages are 24V AC, 120V AC, 240V AC, or even DC voltages. Connecting a 24V coil to a 120V supply will instantly burn it out.
6. Auxiliary Contacts (NO/NC): Determine if you need extra contacts for your control logic. Do you need a signal to light up an indicator lamp? Or do you need to prevent another part of the system from turning on? Our WTAIDQ CJX2N and CJX2D models, for example, come with built-in auxiliary contacts (1NO+1NC) for this very purpose.
7. Certifications (Trust and Safety): Always choose a contactor that is certified by a recognized body. This is your guarantee of safety and quality. Look for marks like UL, CE, TUV, or CSA. These certifications ensure the product has been rigorously tested to meet industry standards set by organizations like the National Electrical Manufacturers Association (NEMA).
AC Contactor vs. DC Contactor
While they look similar, you generally cannot use an AC contactor for a DC circuit, and vice-versa. The physics of alternating current (AC) and direct current (DC) are fundamentally different, especially when it comes to breaking a circuit.
Here’s a simple breakdown of the key differences:
Feature | AC Contactor | DC Contactor |
Arc Quenching | Relies on the natural zero-crossing of the current to easily extinguish the electrical arc. | The constant DC current creates a powerful, persistent arc that requires special, robust arc suppression systems (e.g., magnetic blowouts). |
Electromagnet Core | Uses a laminated iron core to reduce eddy currents and prevent overheating. | Can use a solid iron core because eddy currents are not generated by constant DC voltage. |
Shading Coil & Noise | Contains a shading coil to prevent chattering and vibration, which causes a slight, normal humming sound. | Does not need a shading coil, resulting in silent operation. |
Safety Warning | Cannot be safely used for DC loads. Doing so presents a major fire hazard as the arc may not be extinguished. | Specifically designed and required for the safety of DC applications like solar, battery storage, and DC motors. |
As specialists in new energy, we emphasize this point: for solar PV systems, battery storage, or DC motor drives, you must use a dedicated DC contactor like our WTAIDQ CJX2-Z series. It is designed specifically for the unique challenges of controlling DC power. For more information on electrical safety in the workplace, we recommend resources from official bodies like Google Scholar articles on Electrical Safety.
Conclusion
Electrical contactor is more than just a switch; it is a vital component for the safety, automation, and reliability of countless electrical systems that power our world.
From its powerful electromagnet to its robust contacts and protective enclosure, every part is engineered to manage immense electrical loads with precision and control.
By understanding the key selection factors—voltage, current, poles, utilization category, and certifications—you can confidently choose the right device for your application. Whether you're powering a simple HVAC unit or a complex industrial machine, selecting a high-quality, certified contactor from a trusted manufacturer ensures your system will operate safely and efficiently for years to come.
FAQs
No, this is highly discouraged and dangerous. DC circuits produce a continuous arc that AC contactors are not designed to extinguish, creating a significant fire risk. Always use a dedicated DC contactor for DC loads.
A low hum is normal for AC contactors. However, a loud buzz or chatter often indicates a problem. It could be caused by low coil voltage, dirt or debris in the magnet assembly, or a broken shading coil. The unit should be inspected and likely replaced.
This is defined by its mechanical and electrical life. Mechanical life is the number of switching cycles without a load, often in the millions. Electrical life is the number of cycles under its rated load, which is lower but still typically ranges from hundreds of thousands to over a million cycles for a quality contactor.
Certification is your assurance of safety and performance. Certified products have undergone independent, rigorous testing to ensure they meet strict standards for construction, materials, and electrical safety. Using non-certified components can void equipment warranties, fail electrical inspections, and pose a serious risk to property and personnel.
Post time: Jul-10-2025